Our Mini 4WD development prototype cars are based on Tamiya MINI 4WD Shirokumakko GT (95304) and Tamiya Kumamon MINI 4WD (95281) with MA Chassis. We added a computer, sensors and data storage into the tiny space of the car, plus some bespoke software, while keeping the driver (the bear) in the driver seat. Our enhanced Mini 4WDs enable us to do scientific experiments and measurements that we couldn’t do before.
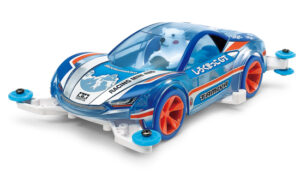
(image source Tamiya website)
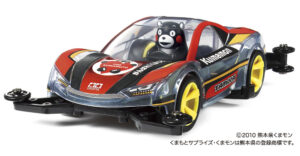
(image source Tamiya Blog)
Technical Spec
Chassis: MA Chassis
Motor: Typically Tamiya Hyper-Dash PRO Japan Cup 2018
Gear Ratio: Typically 4:1 (blue and orange)
Wheel Diameter including tyres: 2.61 cm
Battery: Tamiya Neo Champ 950mAh rechargeable batteries or Eneloop rechargeable batteries
Mass: around 189 grams
Setup: Front and rear carbon fibre stay with 9mm rollers. Full ball bearings.
Brakes: Electronic speed control only. No mechanical or friction type brakes.
Telematics:
- Computer: Based on ATSAMD21 Cortex M0+ 48Mhz processor (Arduino Zero) e.g. Adafruit Feather M0 Basic Proto to run the measuring program.
- Clock: A clock to measure time in milliseconds.
- Sensors:
- 6-axis gyroscope and accelerometer (MPU6050) e.g. GY-521 to measure acceleration and rotation.
- A bespoke designed tachometer to measure distance in centimetres.
- Data Storage: on-board data storage (e.g. Adafruit SPI Flash SD Card 512MB) or on-board MicroSD Card to store the data recorded.
- Electronic speed controller (FET based) driven by software.
- Software: Arduino C/C++, Java.
Motivation
The idea of our enhanced Mini 4WDs came from a dream: “Would it be amazing if our Mini 4WD was able to dynamically and intelligently adjust and optimise its speed according to the track obstacles, track condition and race strategy?”
Given different track obstacles requires different running speed in order to avoid track out or getting stuck, we need a Mini 4WD that can adapt. So in a sense, it is a Mini 4WD car with Artificial Intelligence i.e. A.I. Mini 4WD (ミニ四駆AI in Japanese).
In order to identify the optimal speed for each obstacles, the racer will need to use science and mathematics to find the answer. So rather than relying heavily on trial & error, luck and “experience”, the optimal can be defined, calculated and tested repeatedly in order to get a consistent winning strategy.
As a result, the enhanced Mini 4WD will become a great tool for getting children and adults interested in science, technology, engineering and maths (STEM).
Certainly the concept of an A.I. Mini 4WD car is not new. The idea was illustrated in a Japanese Anime Bakusō Kyōdai Let’s & Go WGP, where the Mini 4WDs were enhanced with an onboard computer, the GP Chip (since 1996).
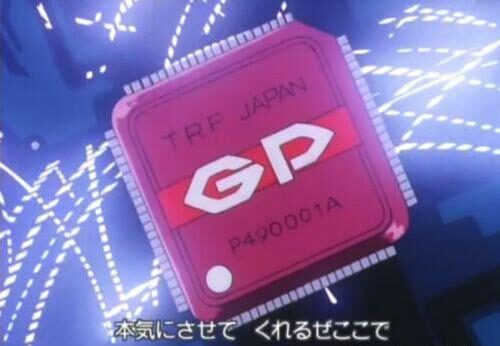
Design Philosophy
AI Assisted: when we included AI features in our Mini 4WDs, the goal was not to replace the racers with AI, but rather using science and AI to help the racer to achieve faster, better and more consistent results.
Enabling feedback loop: traditionally, it is very difficult for a Mini 4WD racer to measure whether a “tweak” brings any improvement. Sometimes the tweak works but often it doesn’t. It is a frustration for many Mini 4WD racers. The goal is to enable the racers to create experiments, do tests and evaluate results. And making it easy for the racers to going through this improvement cycle repeatly. That’s why we developed our Mini 4WDs with the ability to collect telemetry information and we designed graphical tools that enable the racers to visualise the data and make sense of it.
The classic way: we kept the “classic” Mini 4WD racing paradigm i.e. “prepare and race”. Once the car is off, there is no direct human control. It’s all in the setup. It is not an RC car. Sorry no voice control either.
Science it: We would like to see that this new generation of Mini 4WD will become a great tool to encourage children and adults to learn about science, technology, engineering and maths (STEM). People can use the cars to bring science to life and be excited about science.
Development history
The idea of our adaptable Mini 4WD started in 1994. It was based on a mechanical levelling sensor and speed controller. The prototype solution was inspired by some modification ideas came from a Mini 4WD mod guide (see below).
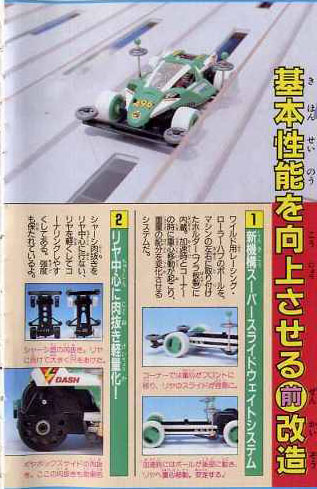
Fast forward to mid 2020. This was when a lot more effort was put into the development. If we want to be able to run experiments with our Mini 4WDs, then the question is: “Is it possible to control the speed of our Mini 4WD with an on-board computer?”
So the first thing was to find out whether it is possible to control the speed of the motor with an Arduino Uno, a variable resistor, a MOSFET and some supporting electronic components.
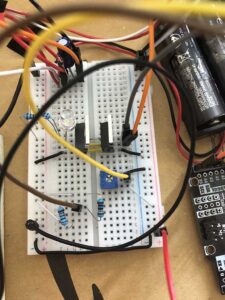
The next challenge was: “How to enable the car to sense its environment so that it can estimate its speed and position?”. This was when we were experimenting with a motion sensor (e.g. the MPU6050) and developing a tachometer.
The next big challenge was: “How can I fit all the electronics into the tiny space of a Mini 4WD”? Measuring up and trying to fit a circuit board in the car.
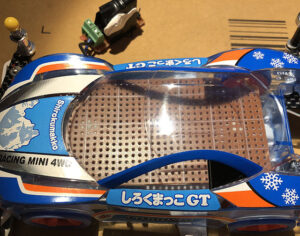
Mark 1 (November 2020)
After several months of exploring, learning and trying. The first Mark 1 prototype was born in early November 2020. It is based on the Tamiya MINI 4WD Shirokumakko GT (95304). It has a computer based on Adafruit Feather M0 Adalogger (ATSAMD21 Cortex M0+ 48Mhz processor Arduino Zero) with a micro SD card for data storage, motion sensor and processor MPU6050 (GY521), MOSFET based speed controller and a custom tachrometer for distance and speed sensing. In this first prototype, the main circuit board was mounted on the MA chassis with velcro!
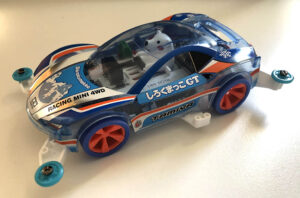
We continue to develop the prototype since then.
Mark 2 (January 2021)
The key improvements on the Mark 2 development prototype were better components connectivity and a more secured way of mounting the computer onto the Mini 4WD. We used Velcro previously as a temporary solution and Mark 2 used standard Mini 4WD screws and nuts.
Mark 3 (February 2021)
There are several major design overhaul with the Mark 3 development prototype, for example, better computer mounting, better tachometer designer with smaller sensors and quick charging access etc… This was also the first time we built the AI car based on the Kumamon Mini 4WD (95281). So we had two AI Mini 4WDs in parallel as we iterated the design. It allowed us to compare the improvement between two generations of designs.
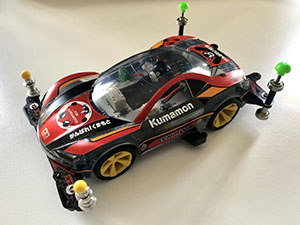
Mark 4 (October 2021)
The major improvement on the Mark 4 development prototype is the use of 3D designed and printed parts. This enabled us to make more suitable and more precise parts for sensor housing and component mounting.
Here is a photo of our Mark 4 development prototype taken at the Makerspace.
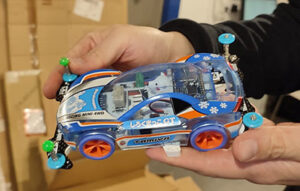
Mark 5 (August 2022)
The biggest change with the Mark 5 development prototype is the use of the Adafruit XTSD 512MB SPI Flash module as the main data storage device and the Adafruit Feather M0 Basic Proto microcontroller as the main computer.
We have been using the Adafruit Feather M0 Adalogger as the main computing module with an on-board MicroSD card storage slot since the beginning. However we noticed that due to the extreme forces and vibration acting on the Mini 4WD during runs, the on-board micro SD card could move and disconnect. This caused the computer to halt. So we decided to experiment with a solid storage option.
In addition, with more precise tooling, the tachometer accuracy was improved to +/- 4mm.
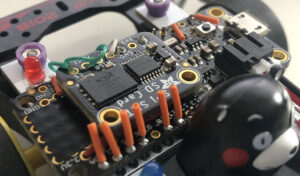
We used this car to run the December 2022 motor experiments as well as to enter the Mini 4WD UK race event in November 2022.
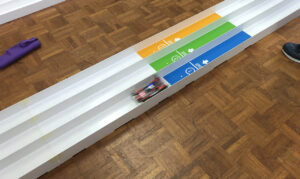
Mark 6 (February 2023)
The design objectives of our Mark 6 prototype car is integration and streamlining.
At the heart of this prototype is our first custom design computer board. We managed to squeeze three major components: motion sensor/processor unit (MPU6050), data storage unit (e.g. XTSD) and main processing unit (ARM Cortex M0+) into a smaller package.
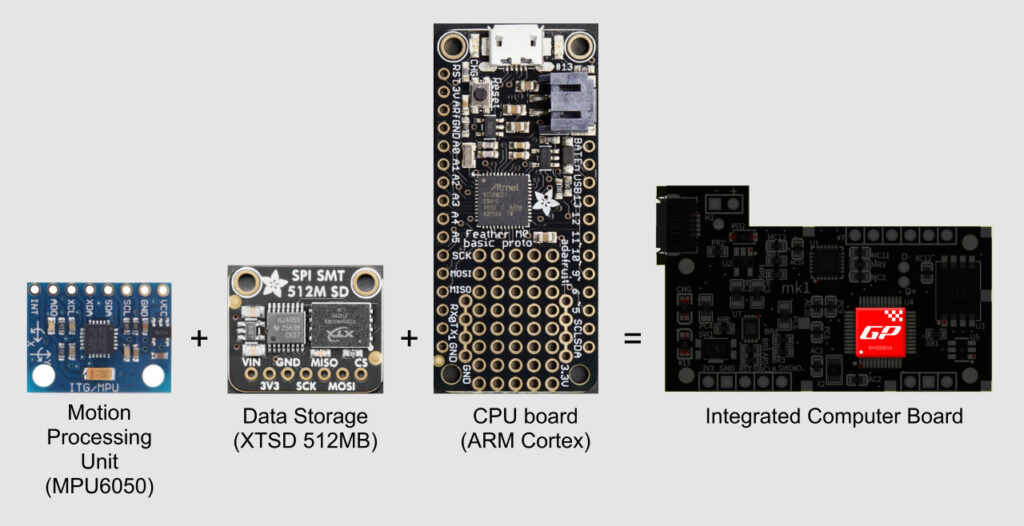
We received our integrated computer boards from the Fab at the beginning of February 2023. The total weight saving so far was around 3g. But the big benefits were better weight distribution, lower centre of gravity and improved reliability (electromagnetic interference reduction).
There were several technical challenges we had to overcome to get it working and we did make a few rookie circuit design mistakes, but we managed to overcome them at the end. Initial tests were promising. We will be running experiments with this new prototype version, and we expect more interesting results. So watch this space.
Mark 6b (March 2023)
We developed a version of the computer board with a MicroSD card slot (in place of an integrated SD memory chip) for our Mark 6b prototype car. The reason behind this change was that we noticed there was a random 100ms+ write delay with the XTSD module. Although 100ms is a small time to us, for the Mini 4WD going at the speed it is going, it is too much. It is almost 10 times slower than our requirements.
We entered a competition with this car. We ran several measurement experiments with it too.
We added a sticker on the processor to match the colour theme. Does it remind you of a Mini 4WD anime?
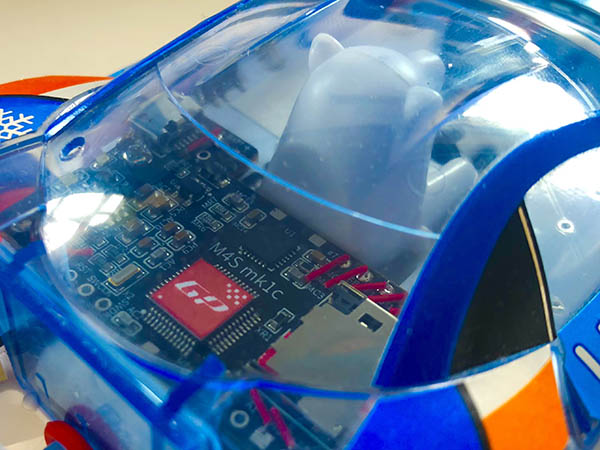
Mark 6c (May 2023)
In May 2023, the next iteration Mark 6c prototype car was born. It uses the same computer board (M4S mk1c) as the Mark 6b car. The major differences are the twin battery design which gives it a better balance and we used more SMD electronic components instead of through hole ones on the main board. The main board design was further streamlined to give it a cleaner and more coherent look.
Mark 6d (June 2023)
With the integrated computer board, we eliminated some Electromagnetic Interference (EMI) issues. But it was still there especially when running Stock and Tuned PRO motors. So we came up with a tweaked designed main circuit board that allowed us to test EMI issues. For example, it enabled us to test splitting and joining ground planes and test signal filters.
After running many experiments, we noticed that splitting ground planes in this application did not give us better results, and sometimes we got worse EMI issues.
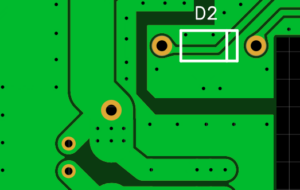
Latest Development
Mark 7 (Aug 2023)
Based on the lessons we learnt from Mark 6d especially in the area of Electromagnetic Interference (EMI) reduction. We redesigned several elements including the mainboard to improve reliability. The Mark 7 car has a lower centre of gravity, thanks to having more components mounted on the bottom side of the mainboard and shorter processor board mounts. The overall new design helps the car to lose around 3 grams of weight and it looks cleaner. We tested the car with various motors in our new Tamiya Mini 4WD 3 Lanes Junior Race Circuit and the results so far are promising. We will continue testing this new prototype and we look forward to running new experiments with it in the near future.
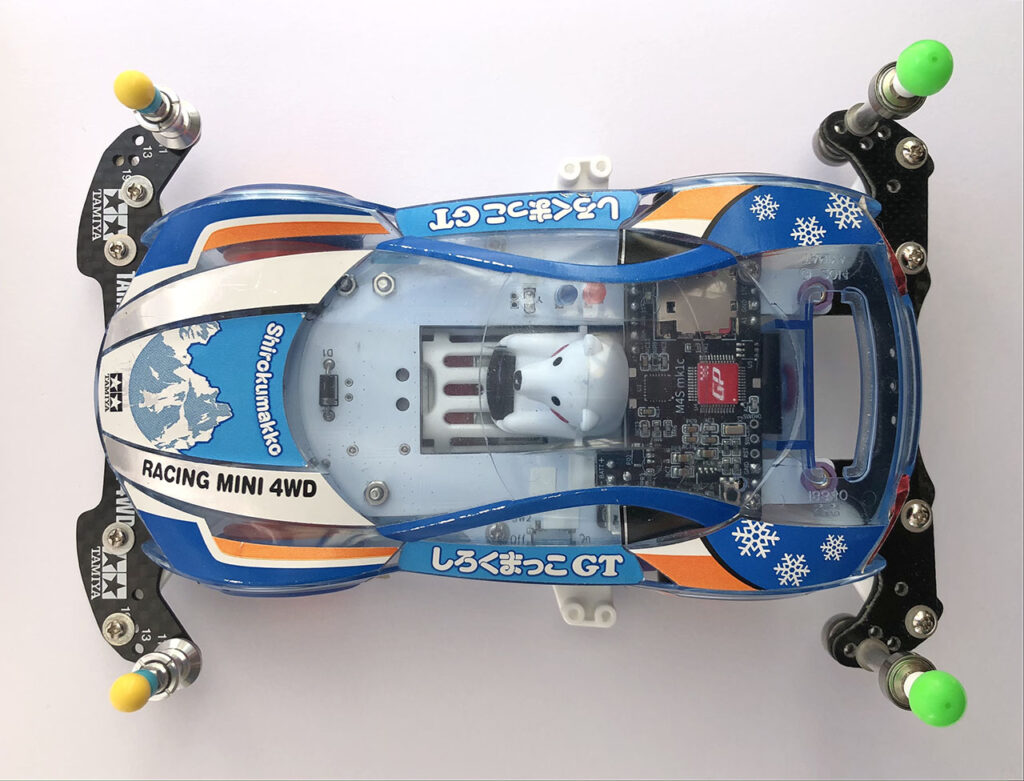
Mark 7b (January 2024)
We noticed that on some rare occasions, the computer in the Mark 7 car could cut out and reset itself, whereas the Mark 6C car doesn’t suffer from the same issue. So we installed a second battery in the spare battery compartment, similar to the twin battery design of the Mark 6C car. As a result, although the Mark 7 car gained an extra 1.5 grams of weight, the cut out/reset problem seems to have gone away.
Mark 8 (February 2025)
Based on feedback and the lessons we learnt from previous generations, we had undergo a major design overhaul on the computer module for the Mark 8 car. We swapped the 2 board design that we had in previous 7 generations with a new single board design. This gives us the space we needed to accommodate a Bluetooth communication plug-in module. The new computer module is 10% lighter than Mark 7b. It also gives the car a lower centre of gravity and better front and rear weight distrbution. We tested the car in our Tamiya Oval Home Circuit and it performed very well. With the ability to communicate with the car via Bluetooth, this enables us to create cool new functions and features. We will continue testing this new prototype and we look forward to running new experiments with it in the near future.
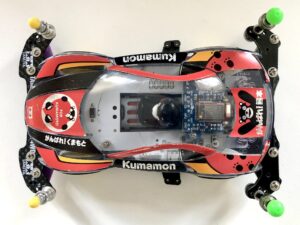
Components we used
- Adafruit Feather M0 Basic Proto
- GY-521 MPU-6050 Module 3 Axis Gyro + 3 Axis Accelerometer Module
- Adafruit SPI Flash SD Card – XTSD 512 MB
#AIMini4WD, #Mini4wd, #STEM, #Tamiya, #ミニ四駆, #ミニ四駆AI, #四驅車, #迷你四驅車