Since the early days of Mini 4WD, Tamiya has been producing different roller upgrades for racers to get the best performance from their Mini 4WDs. The rollers come in different materials, sizes, shapes and colours. Some are standard upgrades, some are HG (High grade) and some are one-off special editions. With some many different ones on offer, the question all racers want to know is… which one is the best? We conducted a scientific experiment to measure the rolling friction of 15 different rollers and ranked them according to their resistance value (roller friction coefficient). We also looked how size, weight, material and shape could affect the performance of these rollers.
Please note this is a live document, it means we will continue updating as we discover more findings from the data. So please feel free to come back and visit again.
Background
Early Mini 4WD cars were mini version of the RC car that Tamiya made such as the famous Hotshot. And these Mini 4WDs came with off road style studded tyres. There are mounting points on the front bumper for rollers or a stay but definitely no rollers mount in mid or rear section of the car. These cars were designed to go around the house over obstacles like books, folders or whatever we could find to build a little obstacle track. So rollers were not important. (Image source Worthpoint)
![Tamiya Mini 4WD Hotshot junior [Item number 2901]](https://www.mini4science.com/wp-content/uploads/2024/07/1_fe69b8ad574b0451054ed64c9cc96013-e1721001159664.jpg)
You can also see a similar setup in the popular comic Dash! Yonkuro (Image source: Wikipedia)
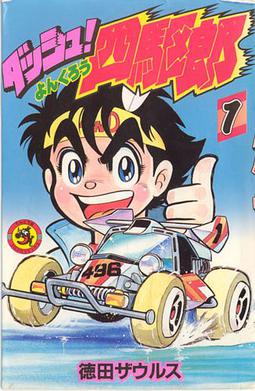
After a short while, a shift of thinking happened and people started to race Mini 4WDs in special race tracks with side walls. Rollers were needed to keep the car running in the track without it damaging the track or climbing over to a different lane. That was the beginning of the rollers era.
Back in the days, the most popular roller upgrade parts came in a pack which contains different colours and sizes. These rollers were made of plastic. They were in red, blue, white and grey etc… and each colour were associated with a certain size e.g. 13mm, 15mm etc… There was no ball race bearing roller back then. All the smooth action was based on grease and oil.
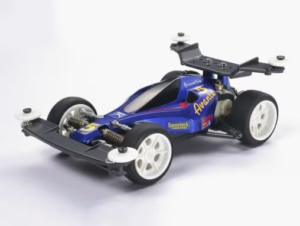
Several years later, metal disc ball race rollers were introduced with a rubber ring. Later metal disc ball race rollers with hard plastic ring, and then followed by ball bearings type and double rollers. More recently metal disc type with flat metal edge type and taper type.
Nowadays, there are so many different types of rollers on offer. It is very hard to know which one is superior or better suited to a certain setup. Hence we conducted this scientific experiment to find some answers and gain valuable insight into picking the best rollers.
Information from the Internet
Here is some of the information we can find on the Internet
“Smaller rollers make your car less stable but quicker in turns. Larger rollers and a wider mounting position make your car more stable but slower in turns. Smaller rollers and a thinner mounting position make your car less stable and faster in turns. A higher roller position makes your car more stable in turns.” from tamiyaracer on WordPress.com
“19’s have faster rolling speed (top speed) compared to 13’s. On the other hand, 13’s have higher rotations per minute making it better low speed/technical stuff. Plus 13mm being closer to the screw makes it in theory more stable during cornering. Though, cornering stability could be compensated with sidewall height (thickness).” from mini4wd forum on Reddit.
There is plenty of anecdotal evidence on the Internet. But yet we can’t find anything that can pass the rigours of science.
Measuring roller friction
Our primary goal was to the measure the roller friction coefficient. The smaller the roller friction coefficient, the less it will affect cornering speed. The higher the roller friction coefficient, the more it will slow down our Mini 4WDs in turns and corners. Let’s explore how we can measure and compare the rollers.
By flicking
Some racers selected their rollers by flicking them on a shaft and timing the duration of the spin. (Video source: Youtube by T-ヒロキ ホビー/T-Hiroki hobby ch)
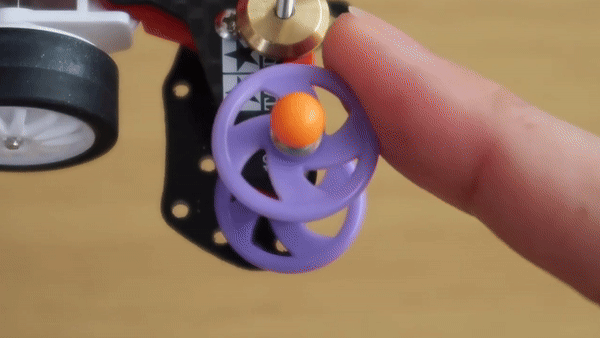
Unfortunately this method is very prone to errors. First the amount of force applied to spinning the wheel can vary a lot by flicking. Secondly timing it by watching the spin is susceptible to observation error including human reaction time. Thirdly, different rollers have different weight, so lighter rollers might not spin as much as a heavier one, due to rotational inertia effect. This is something our readers might have experienced in their childhood when making a spinning wheel with pen and paper (video source: Youtube by Slide Hunt Art). Find out more on ScienceWorld:
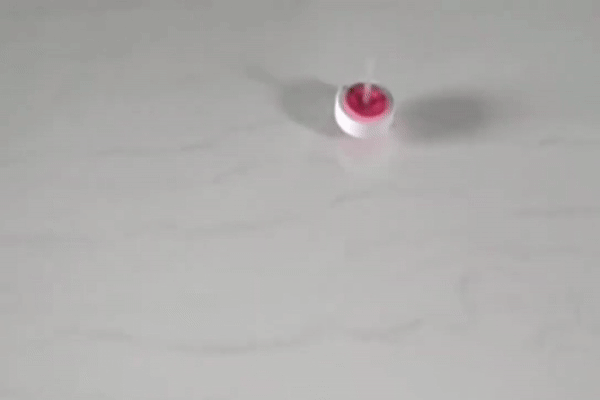
By track testing
Some racers compared rollers by testing them on a track and measuring the lap time. As seen in these videos on Youtube:
- What is the fastest roller!? I tried various types! by T-ヒロキ ホビー/T-Hiroki hobby ch
- Roller Experiment and Analysis by Roscoe Channel
This is a better method and we can see the performance of different setups. However there are many other factors that can have an effect to the overall performance such as tyre condition, battery condition, motor condition and drivetrain condition etc… We noticed this variance in our motor performance measurement experiments before. So it is very hard to proof that it was really the rollers that contributes to the performance change.
A better way?
So is there a better way to measure the roller friction coefficient? Let’s look into science.
The Science
Let’s explore a more scientific approach. The friction of a roller is generated by two things: (1) the friction in the axel and (2) the friction between the roller and the contact surface (rolling resistance). Our Mini 4WD is affected by both of these forces at the same time when cornering so by measuring the overall resistance which is the combination of (1) and (2). We can find out which roller has the least friction, hence is the fastest.
The science of measuring friction on a surface
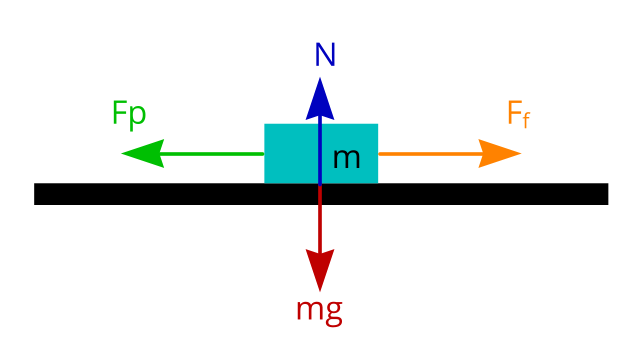
Force is measured in Newtons
m is the mass of the object (in kg)
g is the gravitational acceleration (in metre per second square m/s2). Gravitational acceleration on earth is pretty much constant. We are going to use 9.81 m/s2 in our experiment.
mg is the mass of the object × gravitational acceleration. If an object has a mass of 2kg, then the force acting on the surface through gravity is 2 × 9.81 = 19.62 Newtons
N is the normal force. Since the object is not accelerating downwards through the ground, the ground is exerting the same amount of force (normal force) upwards to keep the object in place, so N is also 19.62 Newtons.
Fp is the force pulling the object to the left. If the pulling force is less than or equal to the frictional force (Fp <= Ff ) the object will not move. But if the pulling force is greater than the frictional force (Fp > Ff), the object will start moving to the left.
Frictional force (Ff) is measured in Newtons.
Frictional force Ff = μ N
Where
μ is the static frictional coefficient (μs) or kinetic frictional coefficient (μk)
N is the normal force (in Newtons).
Static frictional coefficient is measured when the object goes from static (not moving) to moving.
Kinetic frictional coefficient is measured when the object continues to move despite the friction between surfaces but not accelerating or decelerating. E.g. the car keeps sliding at a constant speed.
Therefore:
Frictional coefficient = Frictional force ÷ Normal force ( μ = Ff ÷ N )
Since we can measure m and we know g. We can calculate N as N = mg. If we can steadily increase the amount of pulling force (Fp) until the object starts to move. We can calculate the frictional coefficient.
Hence:
Frictional coefficient = Pulling force ÷ mg
Learn more about friction in our Science 101 friction article here.
So if we design an experiment based on this scientific formula, we can measure the friction coefficient of the rollers. Then we can compare and rank them accordingly.
The Setup
We made a test environment that allowed us to measure the friction coefficient of the rollers.
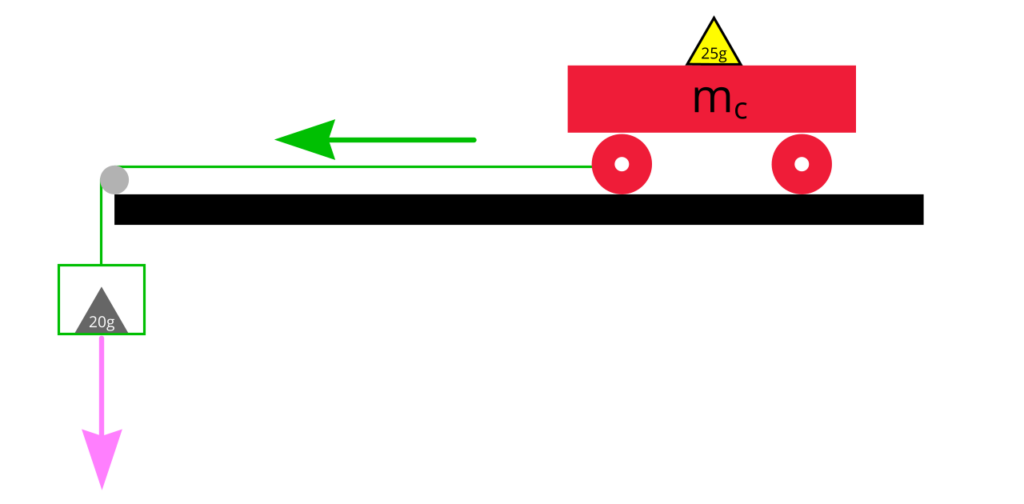
To measure the rolling friction of each set of rollers, we made a custom cart based on standard Mini 4WD upgrade parts. This enabled us to mount four rollers on the cart to run experiments.
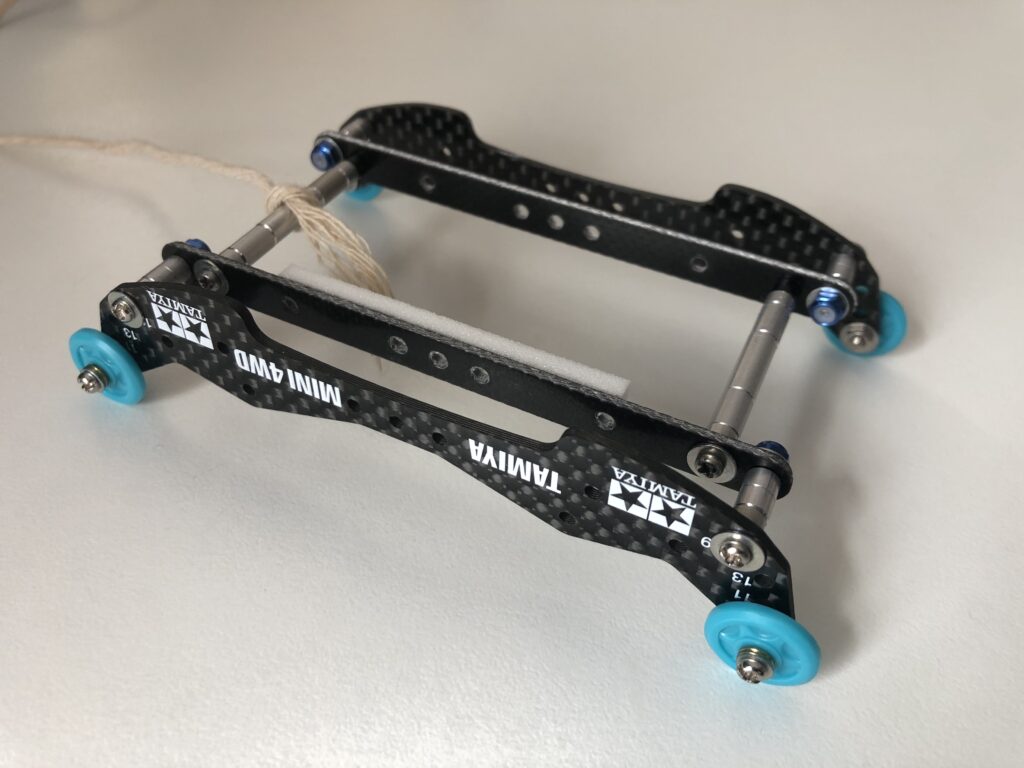
We then put a heavy object on the cart, in this case an old computer harddrive, to add some weight and to create a platform that enabled us to add some more weights so that we could measure the rolling friction of the set of rollers.
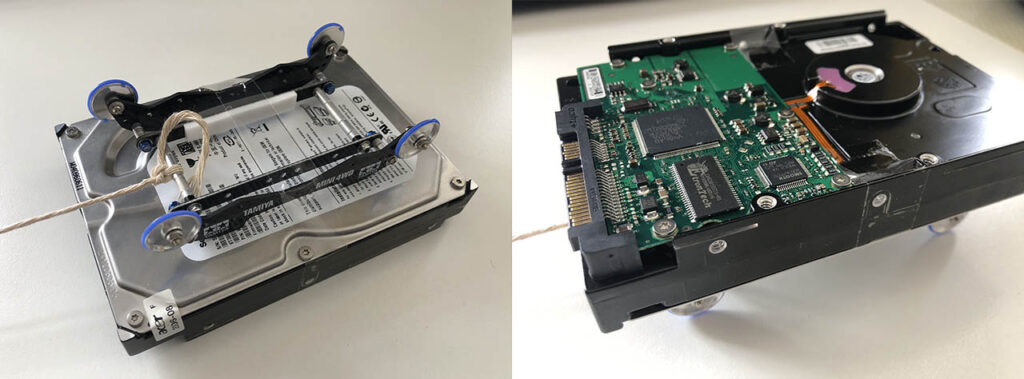
We made a basket (on the left of the diagram) to hold some weights (e.g. Tamiya multi chassis balance weight). The basket was made up of light-weight recycled material and the total mass including part of the rope was around 10.5 grams.
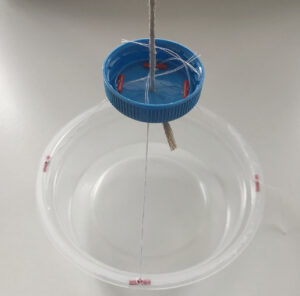
The basket was connected to the cart with a rope passing over a custom made pulley.
By adding weights in the basket, we generated pulling force using gravity. Then we added weights in the basket until the carts started moving in a very slow and steady pace. We recorded the result in a spreadsheet. Unfortunately, since this part was based on observation, there would be a risk of measurement errors. Hence we repeated the experiment several time and used statistical methods to help reduce the errors.
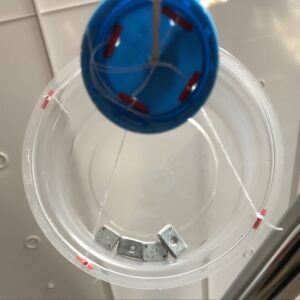
The test surface was based on a Tamiya Junior Circuit straight section.
The pulley was made of a Mini 4WD ball-race double roller to minimise friction. It was supported by FRP fibre glass strips and 3D printed mounts to give it extra strength. It was mounted on our custom made short straight track section.
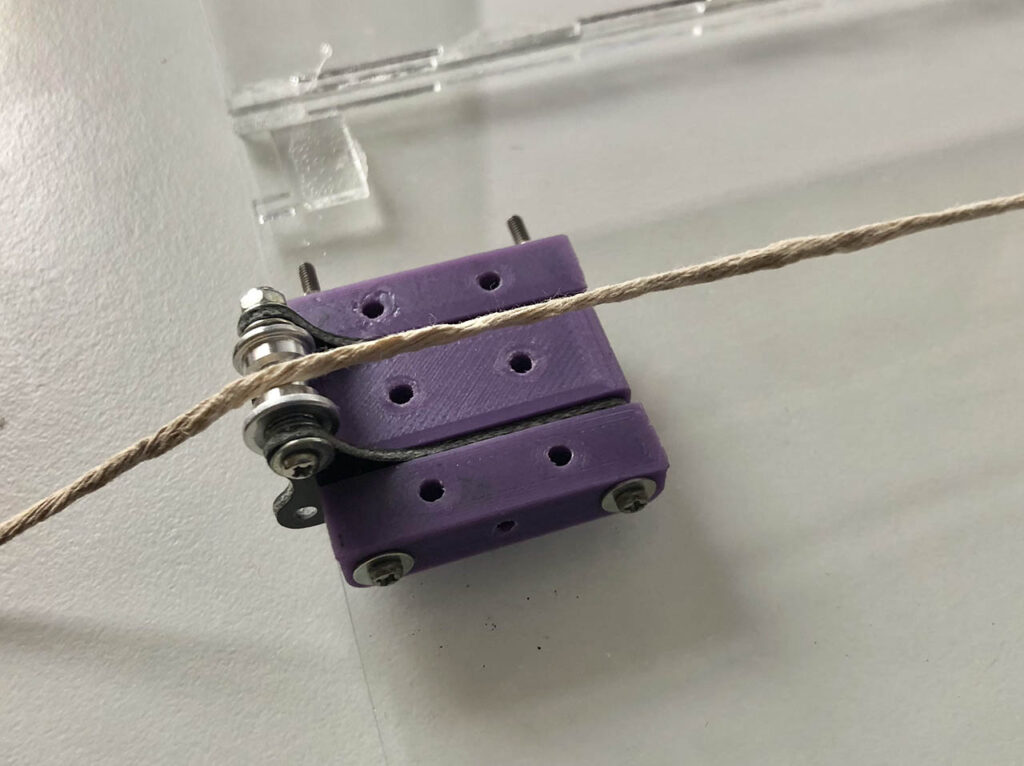
The rope was the strongest and the lightest we could find conveniently in the lab.
For weights in the basket, we were using Tamiya multi chassis balance weight [Item No: 15343] and whatever heavy things we could find on the workbench. This is illustrated as a grey 20g weight in the diagram above.
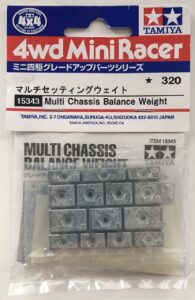
The Forces
Frictional Force
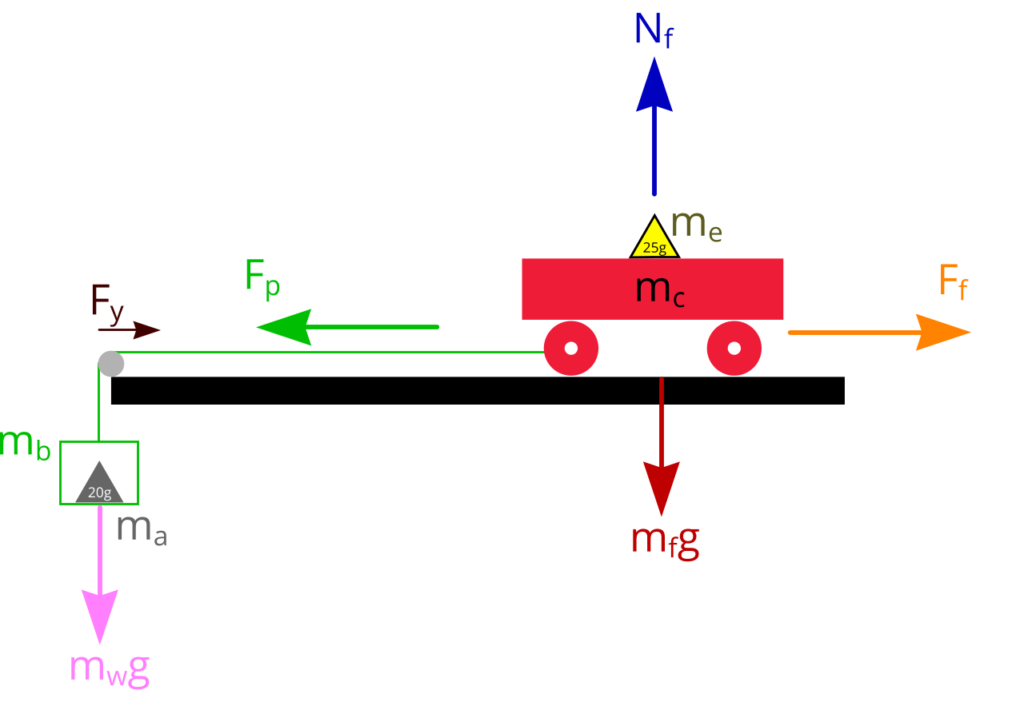
Gravitational acceleration: g = 9.81 m/s2
Mass of the cart (including the harddrive on top): mc
Extra weights on cart (as illustrated by the yellow 25g weight): me
Gravitational force on car is Mfg = ( mass of cart (mc) + mass of the extra weight (me) ) × g
Normal force on 4 rollers: Nf = mfg
Mass of basket: mb
Mass of weights on basket (as illustrated by the grey 20g weight): ma
Total mass on basket: mw = mb + ma
Pulling force: Fp = mwg
Although the formula for frictional force is: Frictional force (Ff) = friction coefficient (μ) × Normal Force (N)
Since we have a pulley in the system there will be a small amount of friction (rolling frictional force) on the pulley. Let’s call this Fy.
Therefore:
Total Frictional Force (Ft) = Frictional force on the rollers (Ff) + Frictional Force on the pulley (Fy).
From previous experiment, we discovered that the Frictional Force on the pulley (Fy) is tiny. Hence we just assumed Frictional Force on the pulley (Fy) = 0;
Therefore:
Total Frictional Force (Ft) = Frictional force on the rollers (Ff) + 0
Ft = Ff
Then
Frictional force (Ff) = friction coefficient of rollers (μ) × force acting on the rollers (mfg)
When Pulling force: Fp > Frictional force (Ff), the cart will start to move. To keep it simple we will just assumed Pulling force (Fp) = Frictional force (Ff) in our calculation.
Re-arranging the formula to get friction coefficient, we get:
Friction coefficient of rollers (μ) = Pulling force (Fp) ÷ Normal force on the rollers ( (mass of cart (mc) + mass of the weight(me) ) × gravity )
Friction coefficient of each roller = Friction coefficient of rollers (μ) ÷ 4
Let’s try to put this into context
According to rolling resistance coefficient examples on Wikipedia, the coefficient of rolling resistance (Crr) of a hardened steel ball bearing on steel is around 0.0010 to 0.0015.
So the friction coefficient of our rollers should be around that range. It also meant we need to add quite a lot of weight on the cart in order to accurately measure the rolling friction of rollers.
Since we know:
Pulling force = mass of object × gravitational acceleration × Frictional coefficient
Suppose the roller frictional coefficient was 0.01 and the mass of cart plus weight was 1kg
Then the force required to pull the cart was 1 × 9.81 × 0.01 = 0.0981N
The mass needed in the basket would be more than 0.0981 ÷ 9.81 × 1000 = 10 grams
Centrifugal force
When our Mini 4WD goes through a turn / corner, there is a centrifugal force that is pushing the car towards the outer wall and the wall pushes back hence the car stays on course and goes around the corner nicely.
The centrifugal force can be calculated with this formula:
Centrifugal Force = mass of car (kg) × velocity of the car (m/s) to the power of 2 ÷ radius of the turning circle (metres)
Fc = mcar × v2 ÷ r
The mass of our Mini 4WD (mcar) is around 189 grams (0.189kg).
We know the size of the track and the radius of the turning circle per lane, starting from inner lane with radius of 36.1 centimetres and each lane outwards will add another ~11.5 centimetres.
For speed, we can consider a range of 2 to 10 m/s based one the result from our motor experiments.
We can simulate the force acting on the rollers by adding weights on the cart, similar to putting the Mini 4WD sideways and add weights on top of it. We can use the Newton’s Law to help us calculate the required weights:
Normal Force (N) = mass (kg) × gravitational acceleration (m/s2)
i.e. FN = m × g
m will be the mass of the car with the weights (meqv)
g = 9.81 m/s2
If we combine the formula together, we can calculate the weights required to simulate the centrifugal force acting on the rollers:
FN = Fc
Therefore
meqv × ag = mcar × v2 ÷ r
meqv = mcar × v2 ÷ r ÷ ag
Since ag is g
meqv = mcar × v2 ÷ r ÷ g
Let’s put some numbers in a table and calculate the centrifugal force and mass equivalent value:
Speed (m/s) | Lane | Force (N) | Mass equivalent (grams) |
2 | 5 | 1.1 | 117 |
2 | 4 | 1.3 | 128 |
2 | 3 | 1.4 | 142 |
2 | 2 | 1.6 | 160 |
2 | 1 | 1.8 | 183 |
3 | 5 | 2.6 | 262 |
3 | 4 | 2.8 | 289 |
3 | 3 | 3.1 | 321 |
3 | 2 | 3.5 | 360 |
3 | 1 | 4.0 | 412 |
4 | 5 | 4.6 | 466 |
4 | 4 | 5.0 | 513 |
4 | 3 | 5.6 | 570 |
4 | 2 | 6.3 | 641 |
4 | 1 | 7.2 | 732 |
5 | 5 | 7.1 | 729 |
5 | 4 | 7.9 | 801 |
5 | 3 | 8.7 | 890 |
5 | 2 | 9.8 | 1,001 |
5 | 1 | 11.2 | 1,144 |
6 | 5 | 10.3 | 1,049 |
6 | 4 | 11.3 | 1,154 |
6 | 3 | 12.6 | 1,282 |
6 | 2 | 14.1 | 1,442 |
6 | 1 | 16.2 | 1,647 |
7 | 5 | 14.0 | 1,428 |
7 | 4 | 15.4 | 1,571 |
7 | 3 | 17.1 | 1,745 |
7 | 2 | 19.3 | 1,963 |
7 | 1 | 22.0 | 2,242 |
8 | 5 | 18.3 | 1,865 |
8 | 4 | 20.1 | 2,052 |
8 | 3 | 22.4 | 2,279 |
8 | 2 | 25.1 | 2,563 |
8 | 1 | 28.7 | 2,929 |
9 | 5 | 23.2 | 2,361 |
9 | 4 | 25.5 | 2,597 |
9 | 3 | 28.3 | 2,885 |
9 | 2 | 31.8 | 3,244 |
9 | 1 | 36.4 | 3,707 |
10 | 5 | 28.6 | 2,915 |
10 | 4 | 31.4 | 3,206 |
10 | 3 | 34.9 | 3,561 |
10 | 2 | 39.3 | 4,005 |
10 | 1 | 44.9 | 4,576 |
Table showing the relationship among speed, lane and weight experience
So from the table, we can see that when a Mini 4WD is going through a corning in lane 2 (the 2nd lane from inner) moving at around 5 m/s (e.g. Sprint Dash Pro Motor performance), the rollers will be experiencing centrifugal force that is equivalent to having ~1kg of weight on the car sitting sideways.
We used this insight to select weights for the experiment.
The Test
Measuring rolling friction
We will be testing each set of rollers five times. Starting with the cart + computer harddrive weight and then adding extra weights incrementally.
Here are the 15 sets of rollers that we tested.
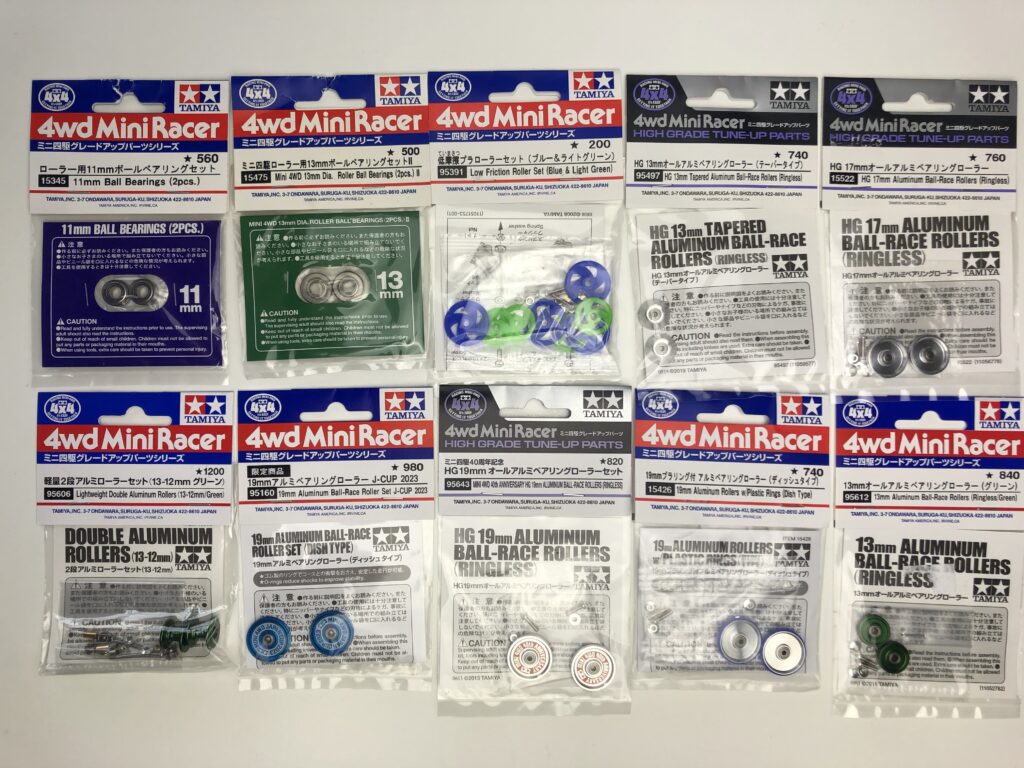
Plastic Roller Type
Kit Standard Roller (13mm/blue) [Item no: 95304]
![Tamiya Mini 4WD Kit Standard Roller (13mm/blue) [Item no: 95304]](https://www.mini4science.com/wp-content/uploads/2024/07/IMG_0670-scaled-e1721002649195-300x102.jpg)
Kit Standard Roller (14mm/yellow) [Item no: 95130]
Low Friction Roller Set Light Green (16mm) [Item no: 95391]
Low Friction Roller Set Blue (19mm) [Item no: 95391]
![Tamiya Mini 4WD Low Friction Roller Set [Item no: 95391]](https://www.mini4science.com/wp-content/uploads/2024/07/IMG_0654-225x300.jpg)
Metal Dish Type
13mm Aluminium Ball-race Roller (Ringless/Green) [Item no: 95612]
HG 17mm Aluminium Ball-race Roller (Ringless) [Item no: 15522]
40th Anniversary HG 19mm Aluminium Ball-race Roller (ringless) [Item no: 95643]
![Tamiya Mini 4WD ringless rollers [Item no: 95612, 15522, 95643]](https://www.mini4science.com/wp-content/uploads/2024/07/ringless-rollers-300x126.jpg)
Metal Tapered Type
HG 13mm Tapered Aluminium Ball-Race Roller (Ringless) [Item no: 95497]
![Tamiya Mini 4WD tapered rollers [Item no: 95497]](https://www.mini4science.com/wp-content/uploads/2024/07/tapered-roller-300x157.jpg)
Metal Dish Type with Rings
19mm Aluminium Rollers w/Plastic Ring (Dish Type) [Item no: 15426]
19mm Aluminium Ball-race Roller Set J-CUP 2023 (blue) [Item no: 95160]
![Tamiya Mini 4WD metal disk rollers with ring [Item no: 15426, 95160]](https://www.mini4science.com/wp-content/uploads/2024/07/rollers-with-ring-300x157.jpg)
Double Aluminium Type
Lightweight Double Aluminium Roller (9-8mm/Red) (new and used) [Item no: 95562]
Lightweight Double Aluminium Roller (13-12mm/Green) [Item no: 95606]
![Tamiya Mini 4WD double aluminium rollers [Item no: 95562, 95606]](https://www.mini4science.com/wp-content/uploads/2024/07/double-rollers-1024x660.jpg)
Ball Bearing Type
9mm Ball Bearing (used) [Item no: 15344]
11mm Ball Bearing [Item no: 15345]
13mm Ball Bearing [Item no: 15475]
![Tamiya Mini 4WD Ball Bearing Rollers 9mm, 11mm, 13mm [Item no: 15344, 15345, 15475]](https://www.mini4science.com/wp-content/uploads/2024/07/IMG_0673-e1721003480570-300x128.jpg)
We were using mostly brand new rollers straight from the packaging and installed them on the cart as they were (with no extra grease or lubricant). Some we had to test with used or a mixed of used and new rollers as we just didn’t have enough. We labelled them clearly in the test results.
To get an accurate picture of the force acting on the rollers we used our precision electronic scale to measure the weight of the cart with the extra weights.
We identified the Pulling force (Fp) required to move the car by adding weights in the basket (ma). We continue adding weights until the car started moving in a very slow and steady pace.
Then we put the weights into our precision electronic scale to measure the total weights (ma) added to the basket. The results (weights on cart (me) and weight on basket(ma) ) were recorded in a spreadsheet.
We calculated the pulling force by adding the weight (ma) and the basket (mb) and then multiply the sum with gravitational acceleration 9.81m/s2.
We calculated the Normal Force by multiplying the weight acting on the cart (weight of car plus the extra weight) with gravitational acceleration 9.81m/s2.
All in all, there will be 15 sets of results from 75 experiments (15 × 5).
Physical attributes
As for the physical attributes of the rollers, here is what we looked into:
Roller diameter: we used a calliper to measure the diameter
Weight: we measured the mass of the rollers, 4 per set, including the mountings with our precise electronic scale. Then we divided the value by 4 to get the mass of each roller with mountings.
Material: we recorded the material of the roller e.g. plastic or metal
Edge thickness: we used a calliper to measure edge thickness
Edge material: we recorded the material of the roller edge e.g. plastic, metal, rubber
Edge Shape: we observed and recorded the shape of the edge e.g. rounded, flat or pointy.
Checks
We checked that the test track was level. We made sure the rope (line) was as level as it could and as straight as it could to minimise errors.
We tested the friction on the pulley from our previous experiment with brake pads and it was tiny. So Fy will be tiny, hence we assumed it to be 0.
We made sure the scale was calibrated before use. We also made sure the scale was reading zero at the start of every measurement.
We made sure the test surfaces (rollers and track) were clean and the cart was pointing as straight as it could.
Assumptions
As mentioned in the checks section, we noticed that the rolling friction of the pulley system was tiny. To keep things simple we will assume that Fy is zero.
To keep things simple, we assumed Frictional force (Ff) = Pulling force (Fp)
Pulling force (Fp) = friction coefficient of rollers (μ) × weight acting on cart (mfg) + Rolling frictional force (Fy)
Becomes:
Pulling force (Fp) = friction coefficient of rollers (μ) × weight acting on cart (mfg)
We used 9.81m/s2 for gravitational acceleration.
Test results
Roller rolling friction
Based on the measurements we captured in a spreadsheet, we calculated the Normal Force and the Pulling force and plotted the result in a chart. We know the formula to calculate coefficient of friction (as state above). We can use linear regression to help us find the best fit line, smooth out some errors and calculate coefficient of friction.
Since we assumed the rolling friction (Fy) on pulley is zero, we could set the y intercept of the linear regression line to zero.
The gradient of the regression line is the friction coefficient of all 4 rollers.
We divided the friction co-efficient value by 4 to give the value of one roller.
We only show the verified friction co-efficient measurement of the 15 rollers in this section. If you would like to see the detail experiment results and charts, please refer to Annex A – Roller friction measurements below.
Now let’s put the experiment result together, plot the data in a bar chart and rank the rollers according to their friction coefficient.
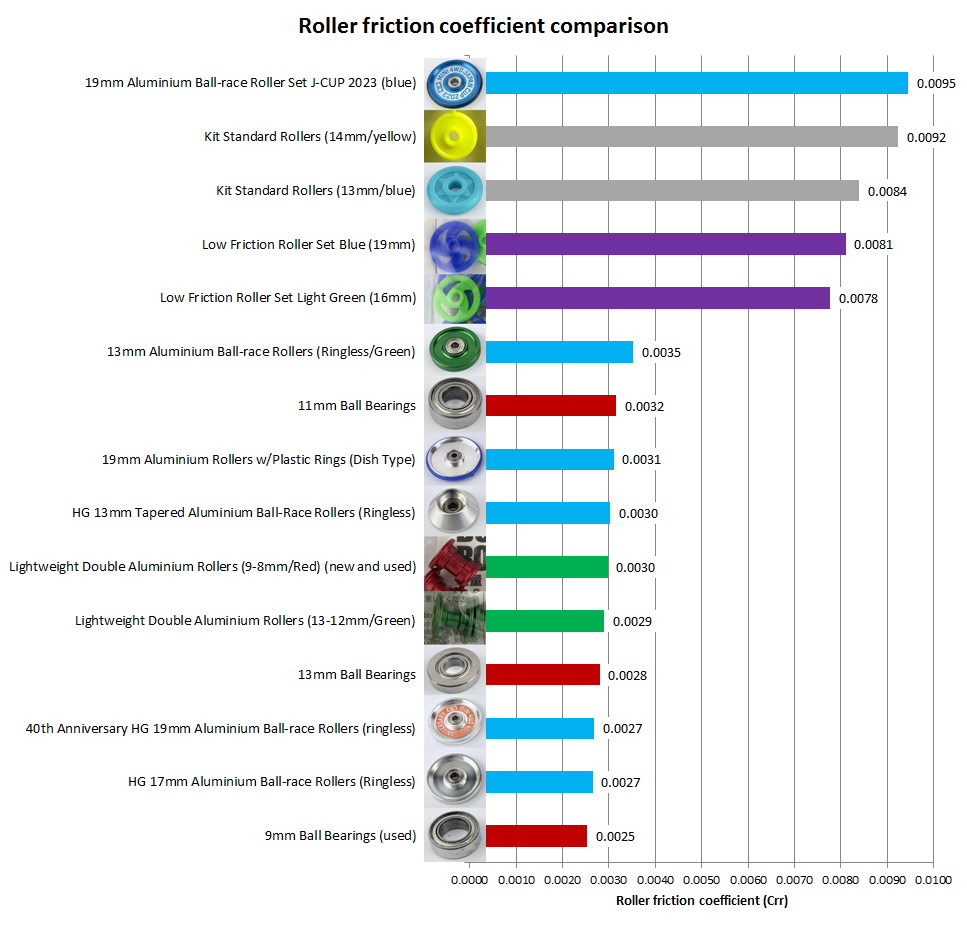
From the experiment, 9mm Ball Bearings had the least rolling friction, hence the fastest. But all-in-all, the metal rollers with ball-race bearing were quite similar to each other with the exception of the 19mm aluminium roller with rubber ring. This roller had even more rolling friction than the plastic rollers and was the slowest in our test.
Talking about plastic rollers, their rolling friction were quite similar to each other with low friction light green being the fastest by a small margin, whereas the ones from a Vanquish VQS was the slowest.
Plastic rollers were on average 2-3 times slower than the metal ones, so metal rollers with ball bearing were definitely a good upgrade choice in general if you would like faster rollers. Low friction plastic rollers will be slow in comparison.
Compare to 9mm ball bearings
If we take the 9mm ball bearings as a base, we can visualise how much slower the other rollers are in comparison.
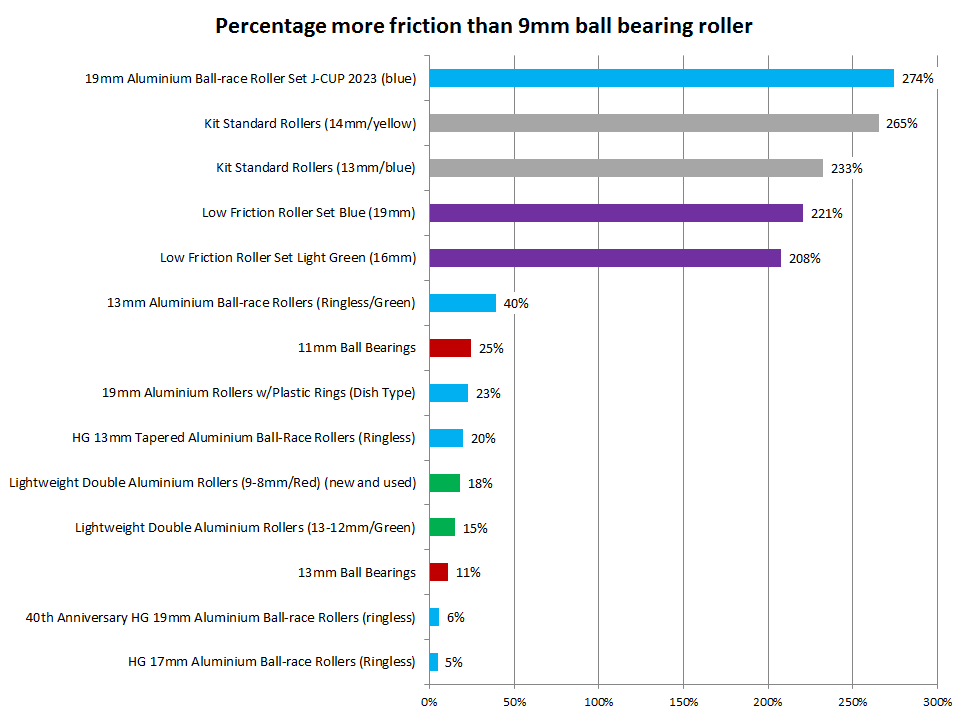
Chart showing the magnitude of rolling friction different rollers in relation to the Tamiya Mini 4WD 9mm ball bearing roller.
So a kit standard roller had around 233% to 265% more rolling friction than 9mm ball bearing roller, whereas 19mm aluminium roller with rubber ring had around 274% more resistance.
Checking physical attributes
We did the measurements and observations as stated before. We put the findings in a table including the roller friction coefficient.
Roller Name | Diameter (mm) | Weight per roller (grams) | Material | Edge Thickness (mm) | Edge material | Edge shape | Roller Friction Coefficient |
Kit Standard Rollers (13mm/blue) | 12.9 | 0.55 | plastic | 0.5 | plastic | round | 0.0084 |
Kit Standard Rollers (14mm/yellow) | 13.9 | 0.44 | plastic | 0.5 | plastic | round | 0.0092 |
Low Friction Roller Set Light Green (16mm) | 15.9 | 0.53 | plastic | 0.5 | plastic | pointy | 0.0078 |
Low Friction Roller Set Blue (19mm) | 19.3 | 0.72 | plastic | 0.5 | plastic | pointy | 0.0081 |
13mm Aluminium Ball-race Rollers (Ringless/Green) | 12.9 | 0.87 | metal + rubber | 2.5 | metal | flat | 0.0035 |
HG 17mm Aluminium Ball-race Rollers (Ringless) | 17 | 1.12 | metal | 2.4 | metal | flat | 0.0027 |
40th Anniversary HG 19mm Aluminium Ball-race Rollers (ringless) | 18.9 | 1.32 | metal | 2.4 | metal | flat | 0.0027 |
HG 13mm Tapered Aluminium Ball-Race Rollers (Ringless) | 13 | 1.00 | metal | 1 | metal | flat | 0.0030 |
19mm Aluminium Rollers w/Plastic Rings (Dish Type) | 19.2 | 1.12 | metal + plastic | 0.5 | plastic | pointy | 0.0031 |
19mm Aluminium Ball-race Roller Set J-CUP 2023 (blue) | 19 | 1.07 | metal | 0.5 | rubber | round | 0.0095 |
Lightweight Double Aluminium Rollers (9-8mm/Red) (new and used) | 9 | 1.10 | metal | 1 | metal | flat | 0.0030 |
Lightweight Double Aluminium Rollers (13-12mm/Green) | 12.9 | 1.75 | metal | 1 | metal | flat | 0.0029 |
9mm Ball Bearings (used) | 9 | 0.98 | metal | 3 | metal | flat | 0.0025 |
11mm Ball Bearings | 11 | 1.65 | metal | 4 | metal | flat | 0.0032 |
13mm Ball Bearings | 13 | 2.29 | metal | 3 | metal | flat | 0.0028 |
Table showing the physical attributes and friction coefficient of each roller
It is quite hard to spot any pattern here. Let’s analysis each attribute separately.
Does diameter size matter?
Let’s compare roller diameter with roller friction coefficient and plot the data in a chart.
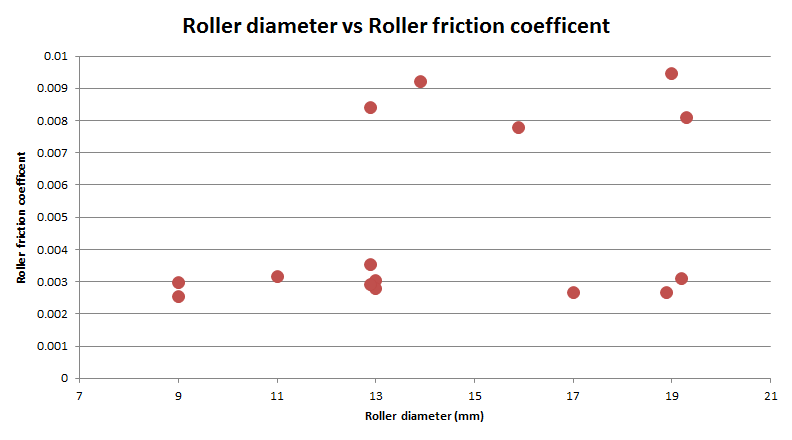
One would think that larger rollers should have less rolling friction. But we couldn’t see this correlation in the chart above. So perhaps the answer is no.
Does weight matter?
Let’s compare weight of roller with roller friction coefficient and plot the data in a chart.
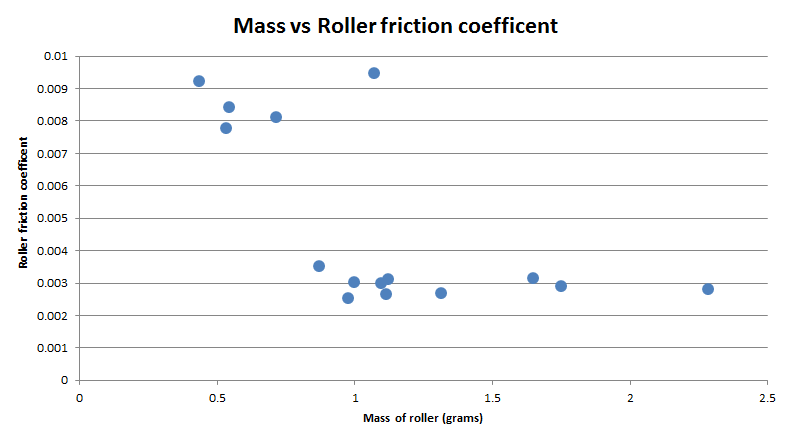
One would think that heavier rollers should have more friction, but we couldn’t see this correlation in the chart above. So perhaps the answer is that mass of roller does not affect its rolling resistance. However scientifically speaking, heavy rollers will reduce your car acceleration and top speed as they will increase the weight of your car.
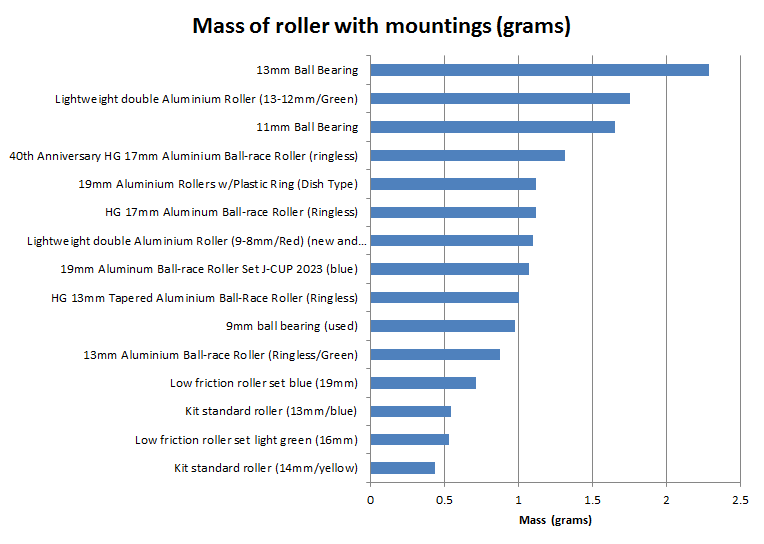
Lotus sports cars are competitive sports cars despite not having super powerful engines as they are designed with light weight in mind, which makes them fast and agile.
Does edge thickness matter?
Let’s compare roller edge thickness with roller friction coefficient and plot the data in a chart.
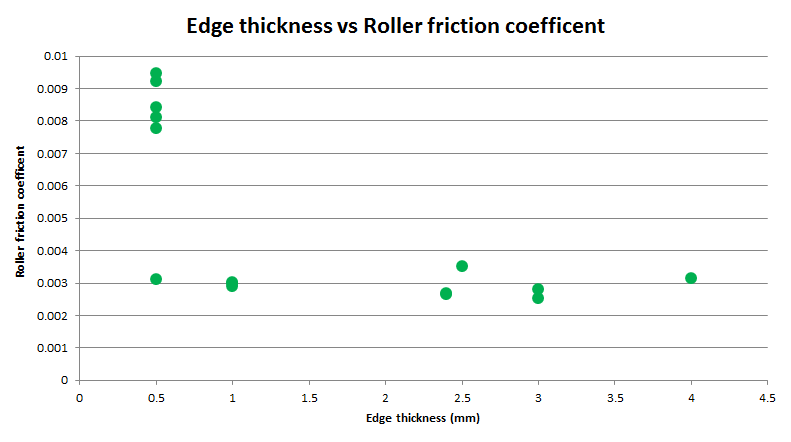
One would think that thicker roller should have more rolling resistance. But we couldn’t see this correlation in the chart above. So perhaps the answer is no.
Does edge material matter?
Let’s compare roller edge material with roller friction coefficient and plot the data in a chart.
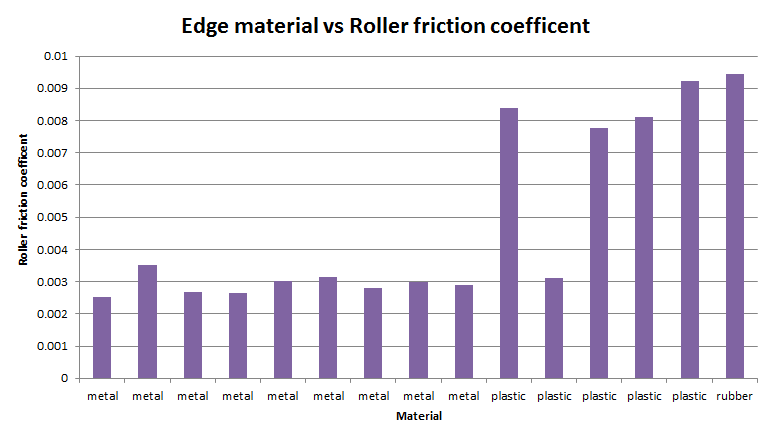
From the chart, we can see that rollers with metal edge were generally faster than those with plastics or rubber.
Amongst the rollers with plastic edge, most of them had 2.5 times more friction than the ones with metal edge except one, which was actually a ball race metal roller with plastic edge. So it seemed like the ball bearing played an important role in reducing rolling friction of a roller.
Rollers with rubber edge had the highest roller friction coefficient despite having a ball race bearing core. So the rubber edge generated a large amount of friction.
Does shape matter?
Let’s compare roller edge shape with roller friction coefficient and plot the data in a chart.
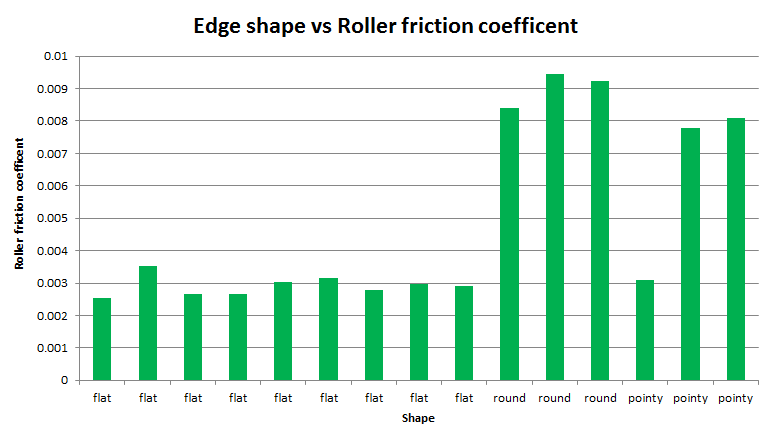
From the chart, we can see that rollers with flat edge were generally faster than those with round or pointy edge.
Let’s look at the data a bit more closely.
Roller Name | Edge shape | Roller friction coefficient |
Kit Standard Rollers (13mm/blue) | round | 0.0084 |
Kit Standard Rollers (14mm/yellow) | round | 0.0092 |
Low Friction Roller Set Light Green (16mm) | pointy | 0.0078 |
Low Friction Roller Set Blue (19mm) | pointy | 0.0081 |
19mm Aluminium Rollers w/Plastic Rings (Dish Type) | pointy | 0.0031 |
19mm Aluminium Ball-race Roller Set J-CUP 2023 (blue) | round | 0.0095 |
Table showing a selection of rollers with round or pointy edge and their roller friction coefficient
We can see our 19mm Aluminium Rollers w/Plastic Rings (Dish Type) had the smallest rolling resistance among the rollers with round or pointy edge, whereas our 19mm Aluminium Ball-race Roller Set J-CUP 2023 (blue) with rubber ring round edge had the highest rolling resistance. The rest were the plastic rollers.
In this case, we could not conclude that the edge shape can affect rolling resistance. But the material such as rubber ring made a big difference.
Important observations from the experiments
When we were aligning the cart, we noticed that metal rollers with flat edge were easy to slide around sideways whereas rollers with pointy edge or rubber ring are much harder to slide. This was even more profound when the cart was loaded with extra weights.
So all in all:
Flat metal edge -> very low friction
Pointy edge has -> more bite
Rubber ring -> most bite
Therefore if you want fast rollers, choose the ones that are made of metal, with ball bearing centre and flat edge. On the other hand, if you need to get more down force with your angled rollers, choose the ones with pointy edge or rubber ring.
What does the result mean to fellow racers?
We found that ball race metal rollers were much faster than kit standard and low friction rollers. All ball-race metal rollers were almost as good as each other in terms of roller friction. Some rollers were heavier and some were lighter. Scientifically speaking, using heavy rollers would reduce your car’s acceleration and top speed.
The surprising finding is that the shape and material of the roller edge are actually two very important factors: Metal rollers with ball bearings and flat edge had the lowest rolling resistance, so they would be more suitable for high speed circuit. Hence you often see people using ball bearing rollers for high speed race. Whereas rollers with pointy edge or rubber ring would give you more down force, so they would be more suitable for technical track where you need more downforce with your angled rollers.
Conclusion
At the beginning of this experiment, we set our goal to find the best roller from the 15 sets of selected Tamiya Mini 4WD rollers in our stock. Most of the rollers were brand new and a few were used.
So which one is the best roller? It depends on your definition of “the best”. If the best means the fastest, then the one with the smallest roller friction coefficient is the fastest. We found that our 9mm ball bearing roller set (used) has the smallest roller friction coefficient at 0.002525, hence it is the fastest among those we tested. Although it was the fastest by measurements, other metal rollers were pretty close too. The differences were so small we probably won’t notice the difference.
Certainly, we don’t know for sure whether a brand new set of 9mm ball bearing rollers would perform the better or worse, but the result does provide a useful indication.
If the best means the one that generates more downforce, then the ones with more sideways grip will be best. We found rollers with rubber ring or pointy edge would give you this benefit.
All-in-all, we found that ball-race metal rollers were generally faster than plastic ones. Roller edge shape and material (e.g. plastic or rubber ring) matter more if you were looking for downforce.
The discovery of the importance of roller edge shape and material gives us the idea that we should design another experiment to measure the friction coefficient of the rollers at an angle so that we can find out the amount of downforce they can generate. So watch this space.
In this experiment, we measured the static frictional coefficient (μs) of the rollers which was when the rollers went from static (not spinning) to spinning. We haven’t measured the kinetic frictional coefficient (μk) which is when the rollers continues to move and rotate despite the friction but not accelerating or decelerating e.g. the cart keeps moving at a constant speed. From observation, the cart seemed to be accelerating when it started moving, so kinetic frictional coefficient should be smaller than static frictional coefficient.
Certainly roller selection, placement and mounting position are important to archieve a good setup. Also, we haven’t looked into how roller’s rotational inertia from rollers weight plays a role in performance. These will be a topic for another time.
The experiment we have done is by no means conclusive. We have yet to test more of the same rollers to get a more accurate measurement average. Your equipment and your experiment might produce slightly different results. However the investigation does give an insight to the performance of different rollers. We hope that it provides you a useful insight to the subject matter.
What would you take away from this experiment? How would you improve it? Please feel free to leave a comment on our Facebook page @Mini4Science or through our contact us page.
Annex A – Roller friction measurements
Charts showing the normal force and pulling force of 15 different roller experiments grouped by type. The R2 values are over 0.91 meaning there is a statistically significant relationship between Normal force and Pulling force.
Plastic Roller Type
Kit Standard Roller (13mm/blue)
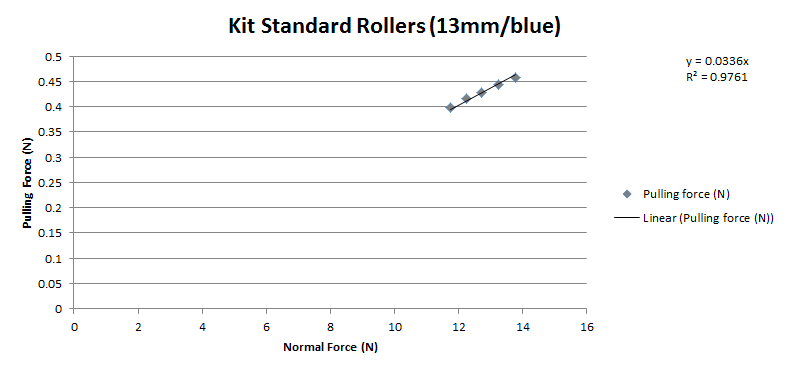
Coefficient of friction of 4 rollers (Average): 0.0336697
Standard Deviation: 0.00002819
Coefficient of friction of 4 rollers (Regression): 0.0336
Coefficient of friction per roller (from Regression): 0.0084
Kit Standard Roller (14mm/yellow)
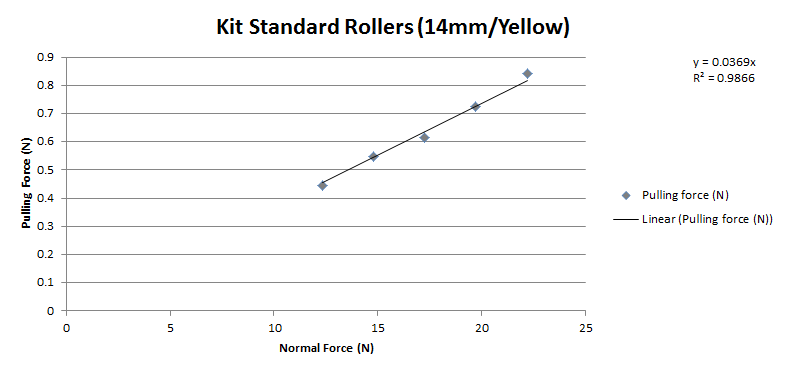
Coefficient of friction of 4 rollers (Average): 0.036641725
Standard Deviation: 0.000927702
Coefficient of friction of 4 rollers (Regression): 0.0369
Coefficient of friction per roller (from Regression): 0.009225
Low Friction Roller Set Light Green (16mm)
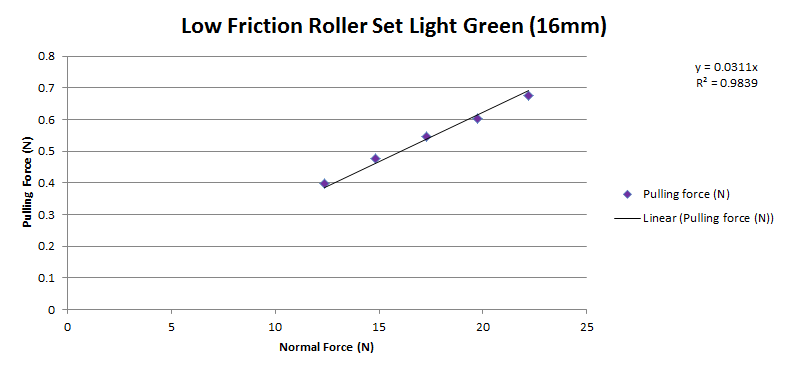
Coefficient of friction of 4 rollers (Average): 0.03141455
Standard Deviation: 0.000812655
Coefficient of friction of 4 rollers (Regression): 0.0311
Coefficient of friction per roller (from Regression): 0.007775
Low Friction Roller Set Blue (19mm)
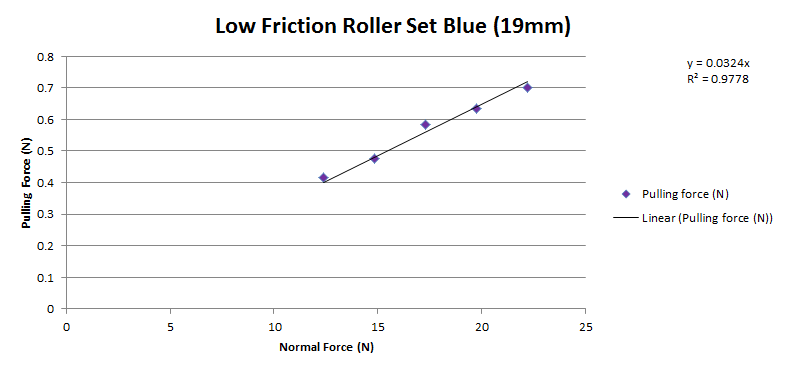
Coefficient of friction of 4 rollers (Average): 0.032625866
Standard Deviation: 0.00101313
Coefficient of friction of 4 rollers (Regression): 0.0324
Coefficient of friction per roller (from Regression): 0.0081
Metal dish Type
13mm Aluminium Ball-race Roller (Ringless/Green)
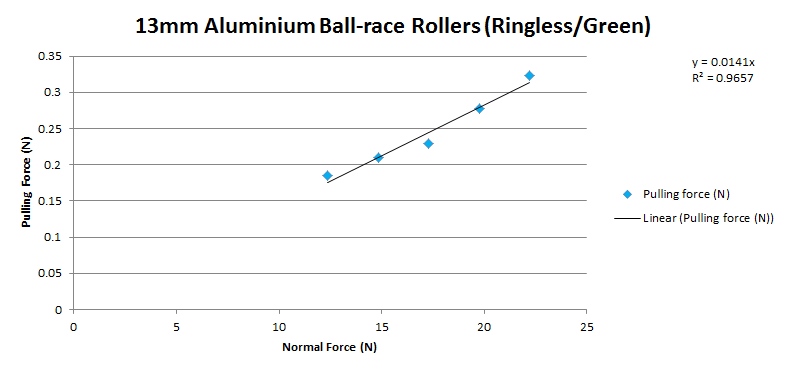
Coefficient of friction of 4 rollers (Average): 0.014174031
Standard Deviation: 0.000630248
Coefficient of friction of 4 rollers (Regression): 0.0141
Coefficient of friction per roller (from Regression): 0.003525
HG 17mm Aluminium Ball-race Roller (Ringless)
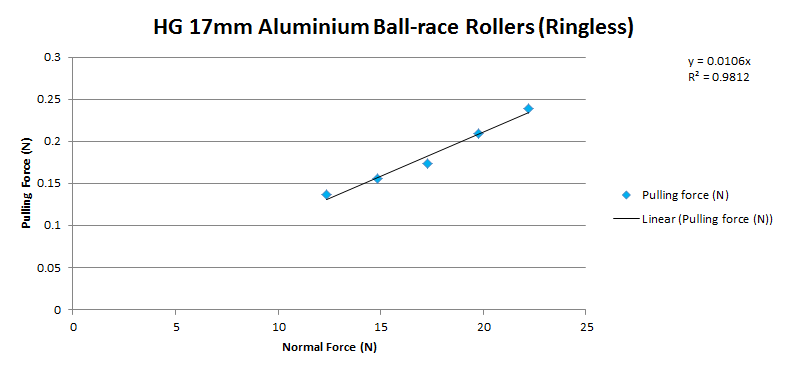
Coefficient of friction of 4 rollers (Average): 0.010591798
Standard Deviation: 0.000358779
Coefficient of friction of 4 rollers (Regression): 0.0106
Coefficient of friction per roller (from Regression): 0.00265
40th Anniversary HG 19mm Aluminium Ball-race Roller (ringless)
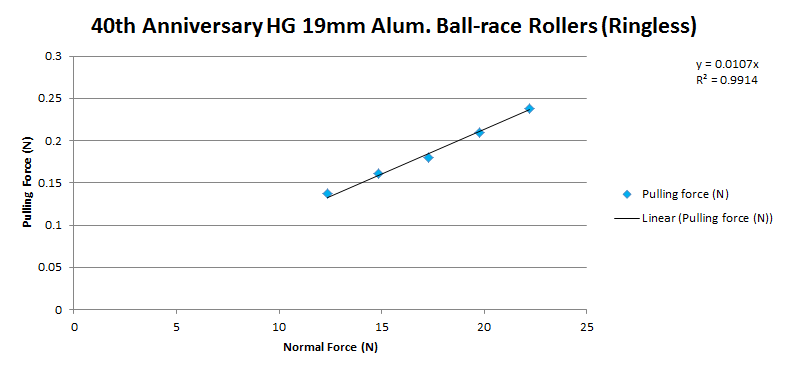
Coefficient of friction of 4 rollers (Average): 0.010712617
Standard Deviation: 0.000249027
Coefficient of friction of 4 rollers (Regression): 0.0107
Coefficient of friction per roller (from Regression): 0.002675
HG 13mm Tapered Aluminium Ball-Race Roller (Ringless)
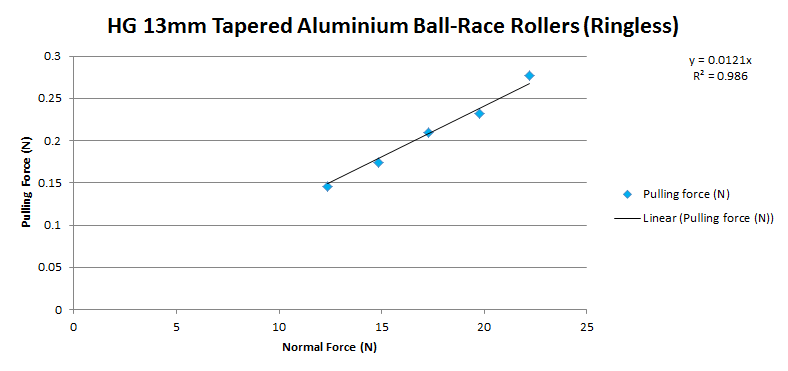
Coefficient of friction of 4 rollers (Average): 0.011976047
Standard Deviation: 0.000304743
Coefficient of friction of 4 rollers (Regression): 0.0121
Coefficient of friction per roller (from Regression): 0.003025
Metal Dish Type with Rings
19mm Aluminium Rollers w/Plastic Ring (Dish Type)
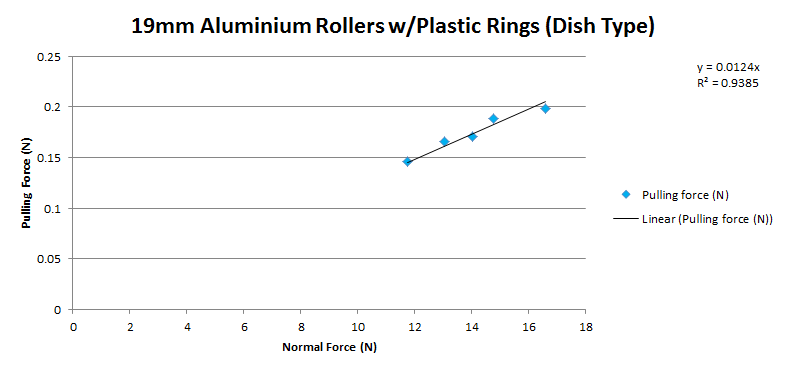
Coefficient of friction of 4 rollers (Average): 0.012395846
Standard Deviation: 0.00033755
Coefficient of friction of 4 rollers (Regression): 0.0124
Coefficient of friction per roller (from Regression): 0.0031
19mm Aluminium Ball-race Roller Set J-CUP 2023 (blue)
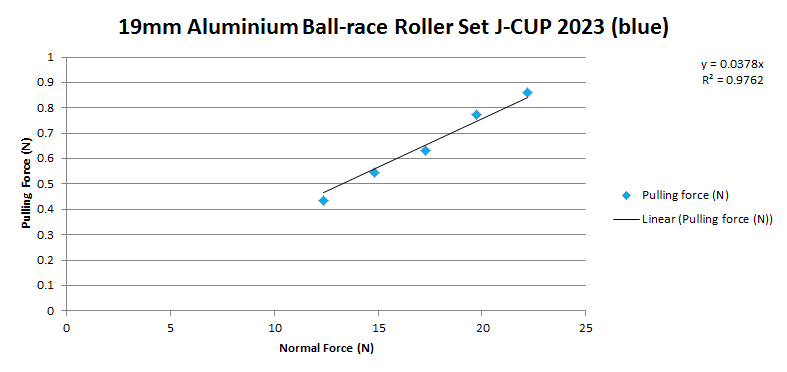
Coefficient of friction of 4 rollers (Average): 0.037282726
Standard Deviation: 0.001617095
Coefficient of friction of 4 rollers (Regression): 0.0378
Coefficient of friction per roller (from Regression): 0.00945
Double Aluminium Type
Lightweight Double Aluminium Roller (9-8mm/Red) (new and used)
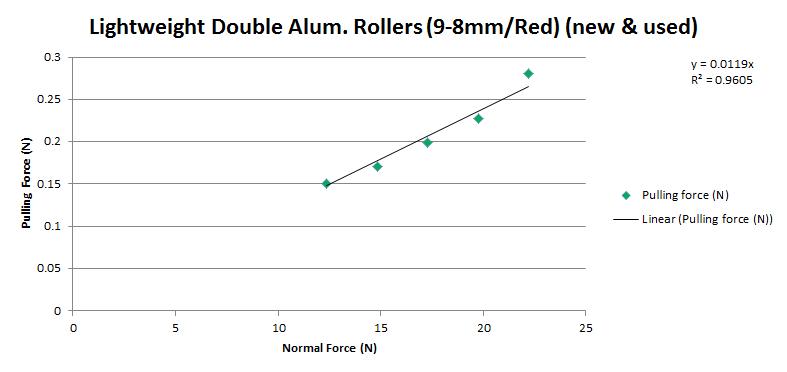
Coefficient of friction of 4 rollers (Average): 0.011880474
Standard Deviation: 0.000515241
Coefficient of friction of 4 rollers (Regression): 0.0119
Coefficient of friction per roller (from Regression): 0.002975
Lightweight Double Aluminium Roller (13-12mm/Green)
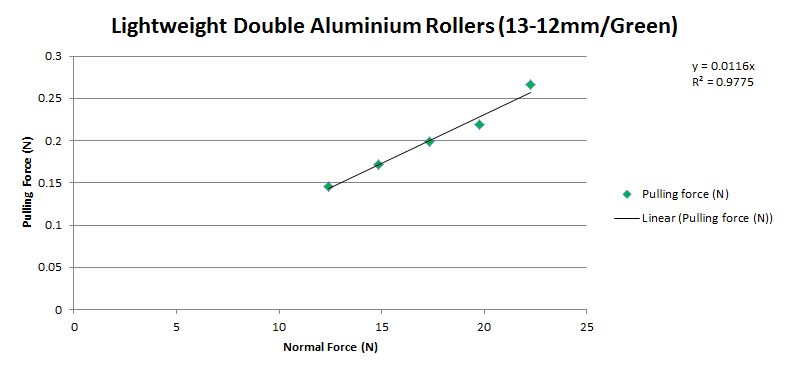
Coefficient of friction of 4 rollers (Average): 0.01155716
Standard Deviation: 0.000344558
Coefficient of friction of 4 rollers (Regression): 0.0116
Coefficient of friction per roller (from Regression): 0.0029
Ball Bearing Type
9mm Ball Bearing (used)
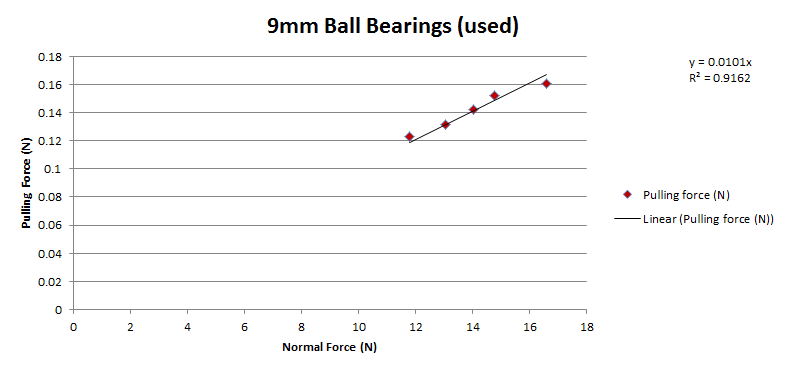
Coefficient of friction of 4 rollers (Average): 0.010126092
Standard Deviation: 0.00029347
Coefficient of friction of 4 rollers (Regression): 0.0101
Coefficient of friction per roller (from Regression): 0.002525
11mm Ball Bearing
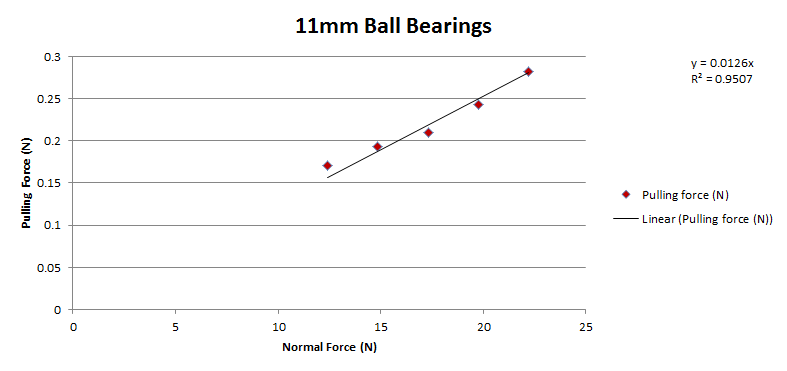
Coefficient of friction of 4 rollers (Average): 0.012763658
Standard Deviation: 0.000670169
Coefficient of friction of 4 rollers (Regression): 0.0126
Coefficient of friction per roller (from Regression): 0.00315
13mm Ball Bearing
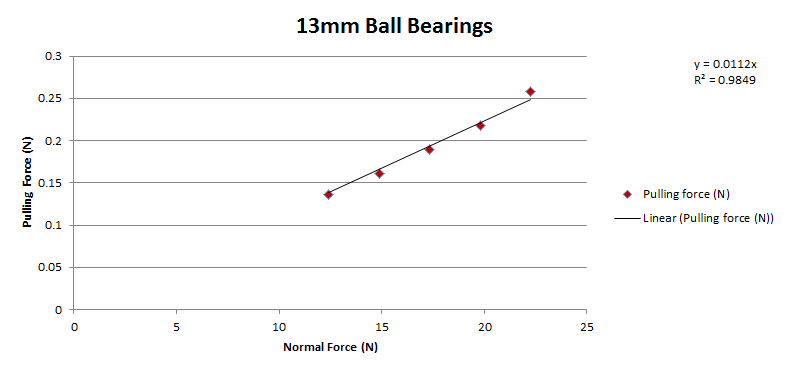
Coefficient of friction of 4 rollers (Average): 0.011071651
Standard Deviation: 0.000291499
Coefficient of friction of 4 rollers (Regression): 0.0112
Coefficient of friction per roller (from Regression): 0.0028